Custom Engineered Precast Refractory Shapes
We specialize in crafting custom-engineered precast refractory shapes designed to meet the rigorous demands of industrial environments.
Precast Solutions
Whether you need structural components like side walls, hearths, car bottom decks, or specialized shapes such as piers, troughs, baffle walls, kiln furniture, or ladle spouts, our team delivers precision and quality every time.
With our dedicated engineering staff, rapid prototyping capabilities, and skilled craftsmen, we ensure you get exactly what your operation needs. No matter your specifications, we can fabricate molds for any precast shape, ensuring each part is durable and built to last.
Why Choose Onex for Precast Refractory Shapes?
Industry-Leading Expertise
Onex has become known for manufacturing long-lasting, durable shapes with superior surface finishes. With in-house experts and a super streamlined process that focuses on engineering and design, our team is an invaluable asset to anyone needing precast refractory shapes.
Precision-Engineered Designs
Our engineering team collaborates closely with you to design shapes that maximize durability and functionality. We leverage unbiased refractory sourcing, ensuring you get the best materials for your specific application, and fabricate shapes with precise mold construction.
Our Proven 5-Step Precast Process
We’ve perfected a step-by-step process to guarantee the quality and longevity of our precast refractory shapes:
STEP 1:
Engineering Design
Our team works with you to understand your needs and develop long-lasting refractory shapes tailored to your operational requirements. We source the best refractory materials to meet your project needs.
STEP 2:
Rapid Prototyping
With advanced technologies, we create high-precision molds using materials like wood, steel, rubber, nylon, and styrofoam, ensuring quick turnarounds without compromising quality. No matter your dimensions, we have the solution.
STEP 3:
Mixing & Vibration
We carefully select refractory materials from a range of manufacturers to ensure the right mix for your application. Our advanced mixers and vibration tables ensure air is removed and the mix is perfectly set.
STEP 4:
Cure & Dry Out
Once the precast shapes are poured, they go through a precise curing process. Afterward, they are dried in our furnaces, which fire up to 2000°F and use slow cool down cycles to ensure each shape sets perfectly.
STEP 5:
Packaging & Shipping
We provide tailored shipping options, offering custom branded packaging to maintain your professional image. Our team carefully packages and schedules deliveries throughout the US, ensuring your parts arrive in perfect condition.
Precast Refractory Shapes Photo Gallery
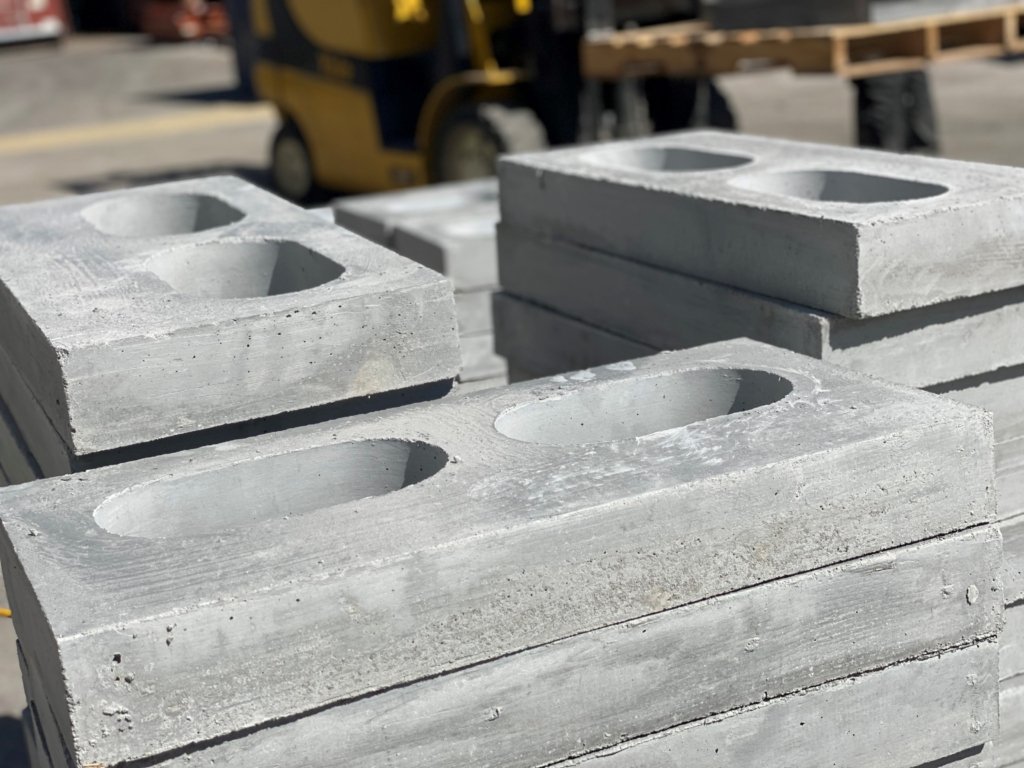
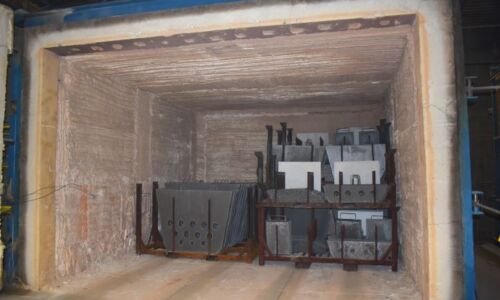
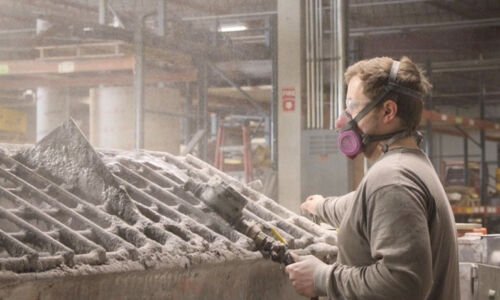

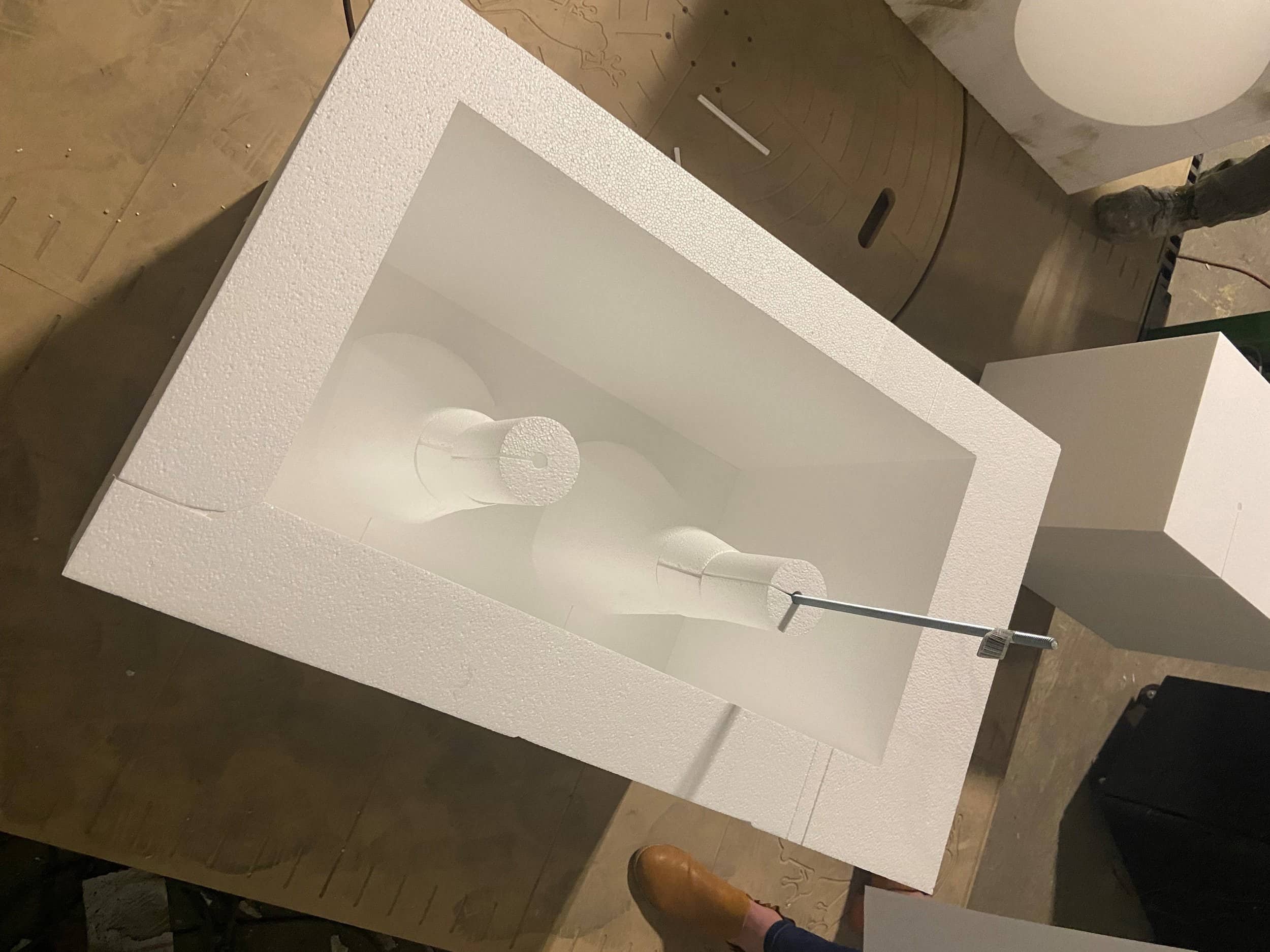
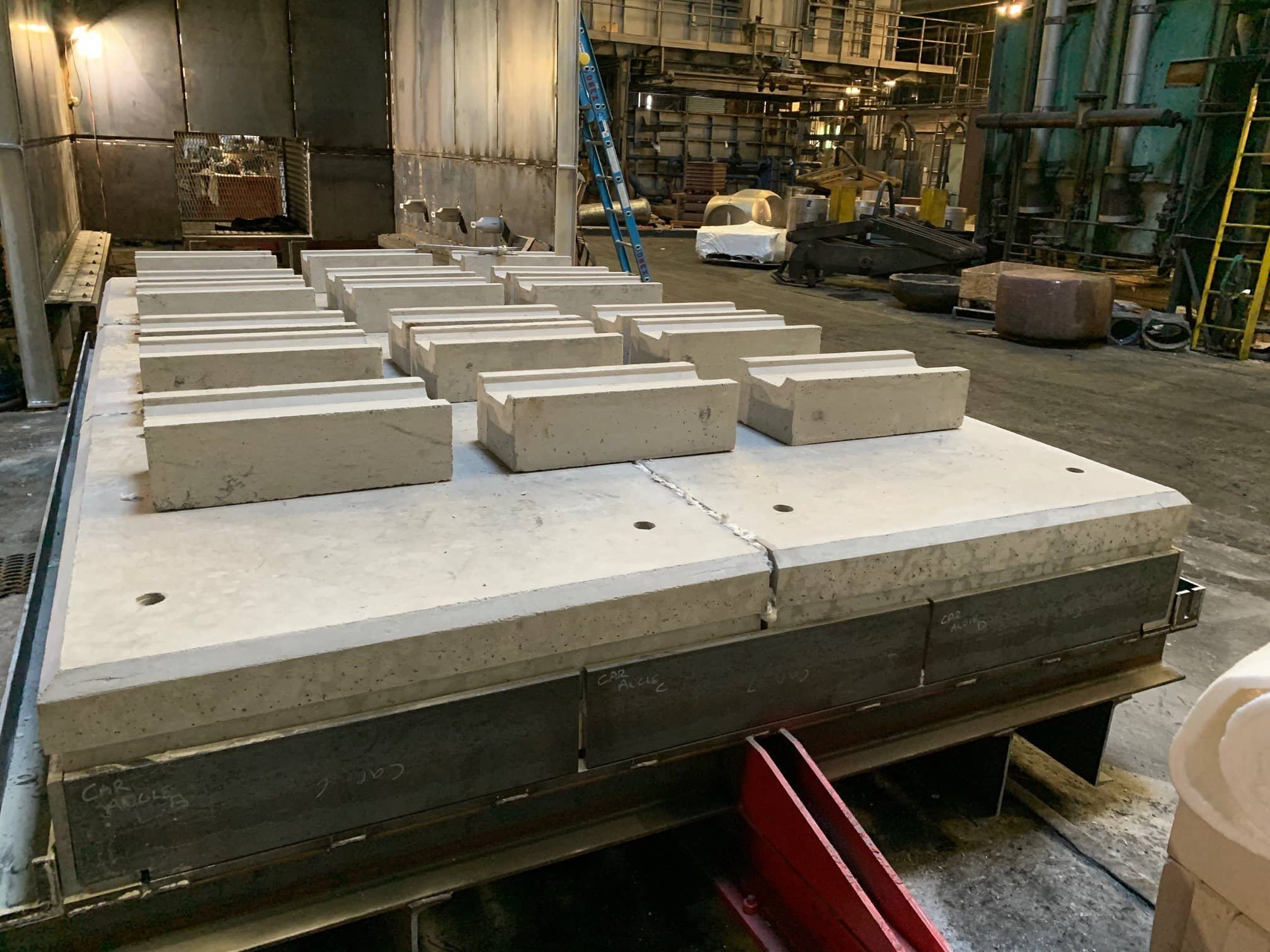
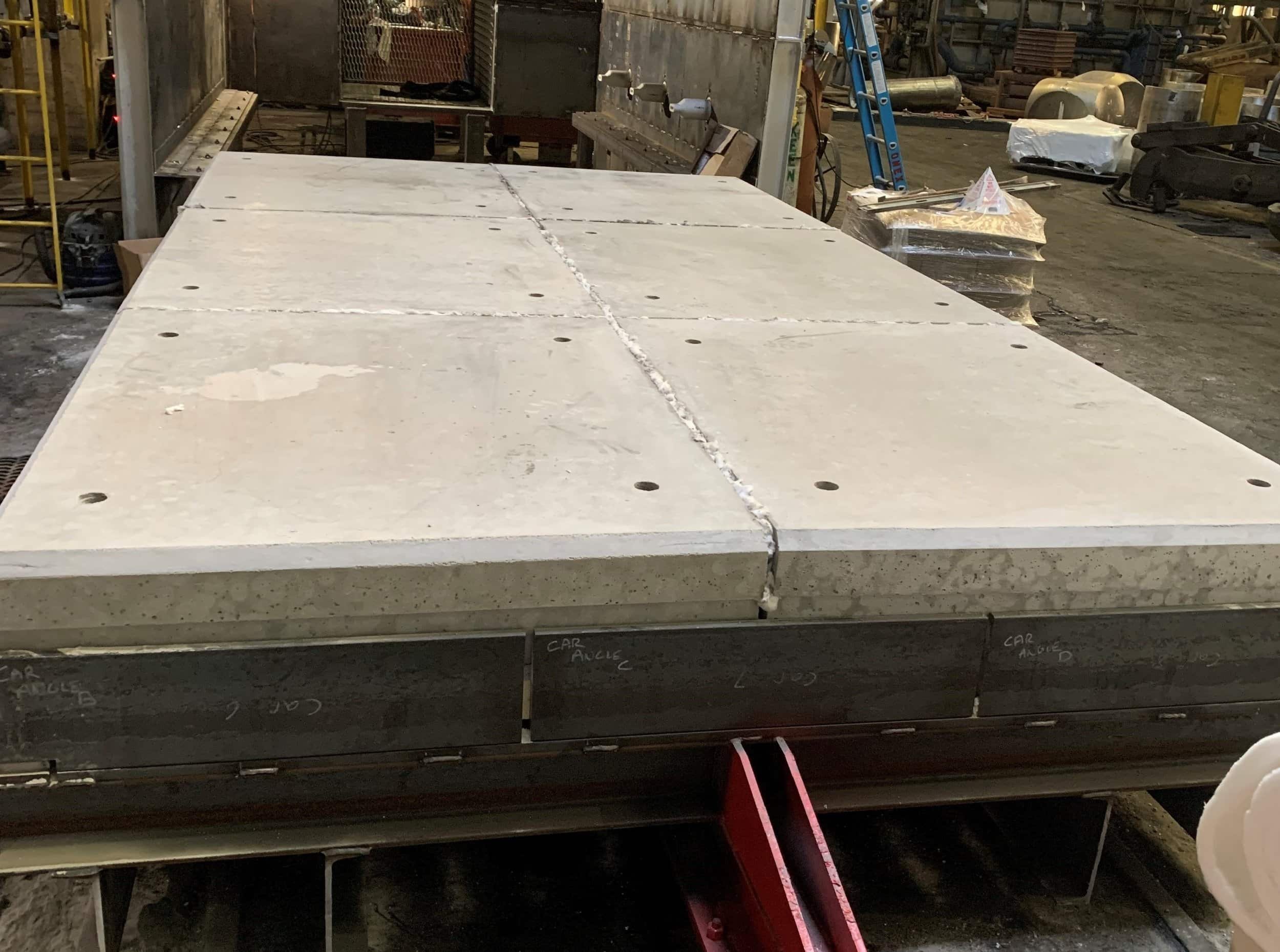
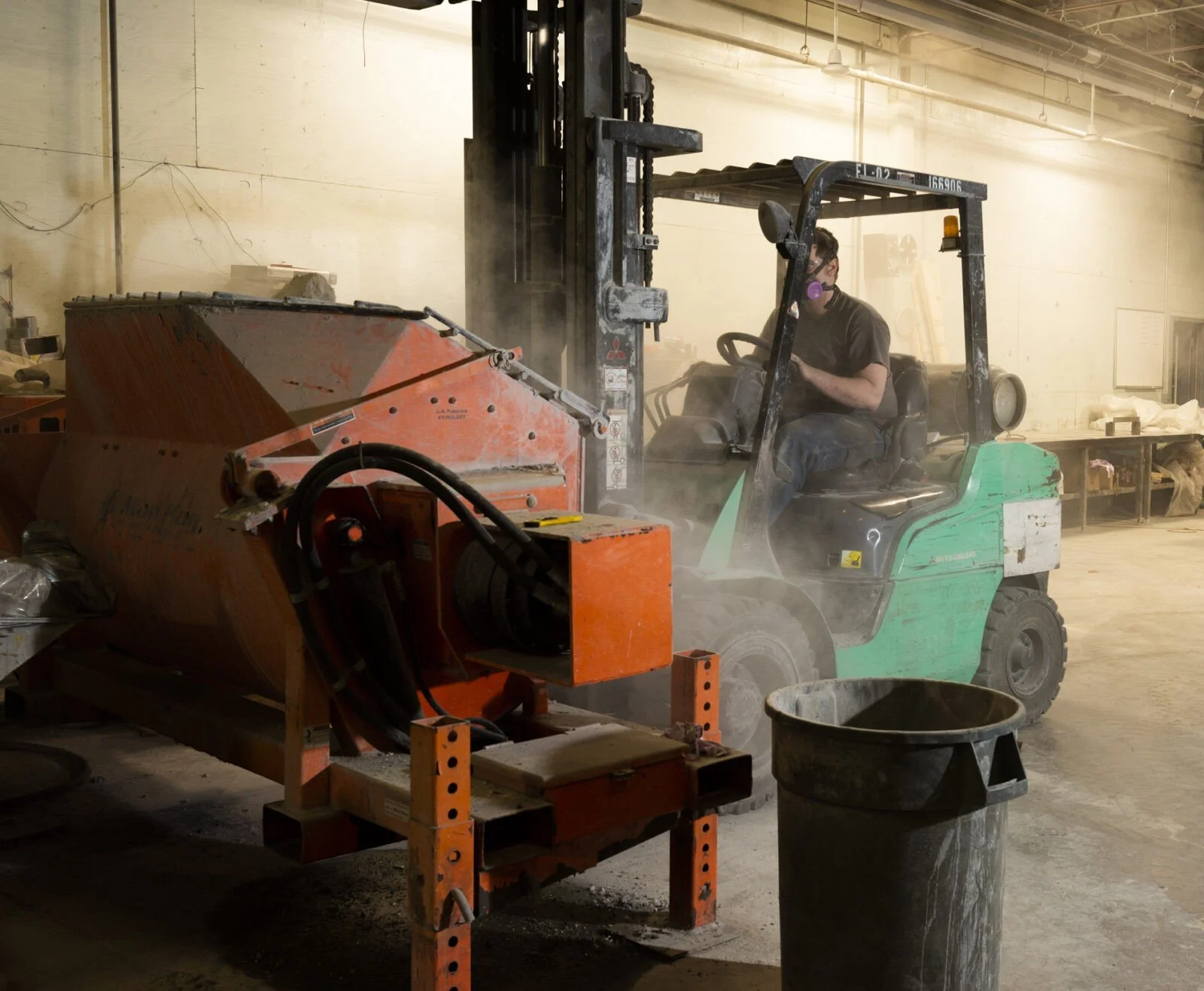